Analyser® – Engineering-KI für die Industrie 4.0
Analyser® – das KI-System für robuste Produkte und stabile Prozesse
Der Analyser® ist ein Engineering-KI-System für Predictive Analytics, Quality und Maintenance, das schon auf Basis weniger Anlernstichproben funktioniert. Es deckt unbekannte Wirkmechanismen und Fehlerursachen in Produkten und Prozessen auf und reduziert in allen Phasen des Produktlebenszyklus‘ Ausschuss, Nacharbeit und Gewährleistungsrisiken um bis zu 60 Prozent.
Das KI-System Analyser® hat sich in zahlreichen Engineering-Projekten und im Fabrikalltag unterschiedlicher Branchen bewährt.
Produktdesign optimieren mit Engineering-KI
Sie sehen gerade einen Platzhalterinhalt von YouTube. Um auf den eigentlichen Inhalt zuzugreifen, klicken Sie auf die Schaltfläche unten. Bitte beachten Sie, dass dabei Daten an Drittanbieter weitergegeben werden.
Werkzeugbau & Validierung optimieren mit Engineering-KI
Sie sehen gerade einen Platzhalterinhalt von YouTube. Um auf den eigentlichen Inhalt zuzugreifen, klicken Sie auf die Schaltfläche unten. Bitte beachten Sie, dass dabei Daten an Drittanbieter weitergegeben werden.
Prozessauslegung optimieren mit Engineering-KI
Sie sehen gerade einen Platzhalterinhalt von YouTube. Um auf den eigentlichen Inhalt zuzugreifen, klicken Sie auf die Schaltfläche unten. Bitte beachten Sie, dass dabei Daten an Drittanbieter weitergegeben werden.
In der Produktion Kosten senken & Qualität steigern mit KI
Sie sehen gerade einen Platzhalterinhalt von YouTube. Um auf den eigentlichen Inhalt zuzugreifen, klicken Sie auf die Schaltfläche unten. Bitte beachten Sie, dass dabei Daten an Drittanbieter weitergegeben werden.
Einsatzgebiete des Analyser®
- Ressourceneffizient vom Prototyp zur Serie mit Engineering-KI –
Ressourcen, Material und Energie in Entwicklung und Produktion einsparen - Produktdesign: Mit Engineering-KI neue Produkte nachhaltig absichern –
schneller fehlerfreie Produkte entwickeln und validieren - Industrialisierung: Mit Engineering-KI sicher vom Prototyp zur Serie –
Qualität verbessern, Kosten und Zeit einsparen - Serienproduktion: Mit Engineering-KI Probleme in der Produktion nachhaltig lösen –
unbekannte Fehlerursachen erkennen und beseitigen - Produktionsunterstützung: Mit Engineering-KI die Produktion 24/7 optimieren –
die „immer- Vor-Ort-Lösung“ gegen Produktionsstopps - Wartung: Mit Engineering-KI Maschinen und Anlagen präventiv warten –
mit Predictive Maintenance Wartungs- und Verschleißdaten zuverlässig vorhersagen
Steht Ihr Fertigungs- oder Entwicklungsteam auch vor diesen Herausforderungen?
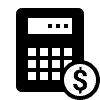
Erhöhte Kosten für Fehler, Nacharbeit und Gewährleistung
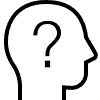
Ursachen für Fehler- und Gewährleistungsrisiken werden nicht erkannt, Maßnahmen laufen ins Leere
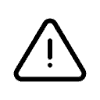
Fehler in Entwicklung, Serienanlauf und Produktion werden nicht (schnell genug) erkannt
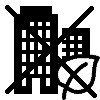
Ausschuss führt zu einem erhöhten Ressourcen-, Material- und Energieverbrauch
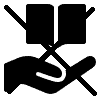
Kostenintensive Produktionsstopps & intransparentes Unternehmenswissen
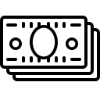
Hohe Herstellkosten hemmen Konkurrenzfähigkeit
Unsere Lösung für Sie
Mit der Engineering-KI-Software Analyser® und unserer praxisbewährten Methode Robust Design erreichen Sie fehlerfreie, robuste Produkte und stabile Prozesse.
Der Analyser® kommt branchenübergreifend in Entwicklung, Produktion und Montage zum Einsatz und verarbeitet dabei alle Produktvalidierungs- und Prozess-Kurven sowie Einzelwerte aus Sensordaten. Für die Modellbildung verwendet der Analyser® die leistungsfähige Software Visual-XSel (www.crgraph.de).
Die zwei Module des Analyser® bieten die passenden Lösungen:
Fehler, Ausschuss und Gewährleistungsrisiken in der Produktion minimieren
Der digitale Produktionsassistent
Der Analyser® deckt vollautomatisch und in Echtzeit Fehler sowie Ursachen auf und liefert anschließend Lösungen und Maßnahmen bei fehlerhaften Produkten und Prozessen. Somit ist der Mitarbeiter im Werk – beispielsweise bei einer fehlerhaften Verschraubung oder Verpressung – in der Lage, gezielt die vom KI-System vorgeschlagenen Maßnahmen zu ergreifen. Denn der Analyser meldet dem Mitarbeiter das Fehlerbild, seine Ursachen und die dazugehörigen Lösungs-Maßnahmen innerhalb von Sekunden.
Zusätzlich enthält er auch ein Selbstlernmodul bei dem erfolgreiche Maßnahmen rückgemeldet werden. Diese Rückmeldungen werden dann bei weiteren Analysen berücksichtigt. Somit verbessert sich ständig die Analyse des KI-Analyser mit Hilfe der Mitarbeiter und Experten (Closed-Loop für Lessons Learned).
Die Vorteile auf einem Blick
![]() |
![]() |
![]() |
![]() |
Schnelle und gezielte Maßnahmen anstatt kostenintensiver Produktionsstopps |
Unterstützung der Mitarbeiter in Echtzeit |
Reduktion von Ausschuss, Fehler- und Nacharbeitskosten, sowie Gewährleistungsrisiken |
Unterstützung bei der Prozessparametrierung bei Produktneuanläufen & Prototypen |
Ursachen der Kosten- und Qualitätsprobleme aufdecken
Der Predictive Modeller
Selbst Experten sind manchmal ratlos und können die Ursachen für Ausschuss, Fehler, Nacharbeit sowie Qualitäts- und Gewährleistungsthemen (teilweise) nicht aufzeigen. Das Problem ist die fehlende Kenntnis über Wirkzusammenhänge und vor allem deren Wechselwirkungen innerhalb von Komponenten, Baugruppen und Herstellprozessen. Der Analyser® erweitert das Wissen, indem er unbekannte Wirkzusammenhänge aufdeckt und in Transferfunktionen speichert. Die Transferfunktion enthält nun alle wichtigen Einflussfaktoren und ihre Wirkungsweise auf das Produkt bzw. den Prozess.
Nun können alle Produkt- und Prozessparameter so gesteuert werden, dass die Qualitätsmerkmale nachhaltig erreicht werden. Durch die Kenntnis der Wirkzusammenhänge können die Herstellkosten nachhaltig gesenkt werden, indem zu enge Toleranzen der Bauteil- und Produktionsparameter geöffnet werden. Die Transferfunktion des Analyser® dient sogar als Vorhersagemodell – damit können Fehler erkannt und beseitigt werden, noch bevor sie entstehen. Der Analyser® wird daher auch für Predictive Analytics und Predictive Maintenance Themen genutzt.
Die Vorteile auf einem Blick
![]() |
![]() |
![]() |
![]() |
Steigerung der Ressourcen-, Material- und Energieeffizienz |
Reduzierung der Produkt-Herstellkosten durch Öffnen der Toleranzen |
Reduktion von Ausschuss, Fehler- und Nacharbeitskosten, sowie Gewährleistungsrisiken |
Absicherung von Entwicklung und Serienanlauf |
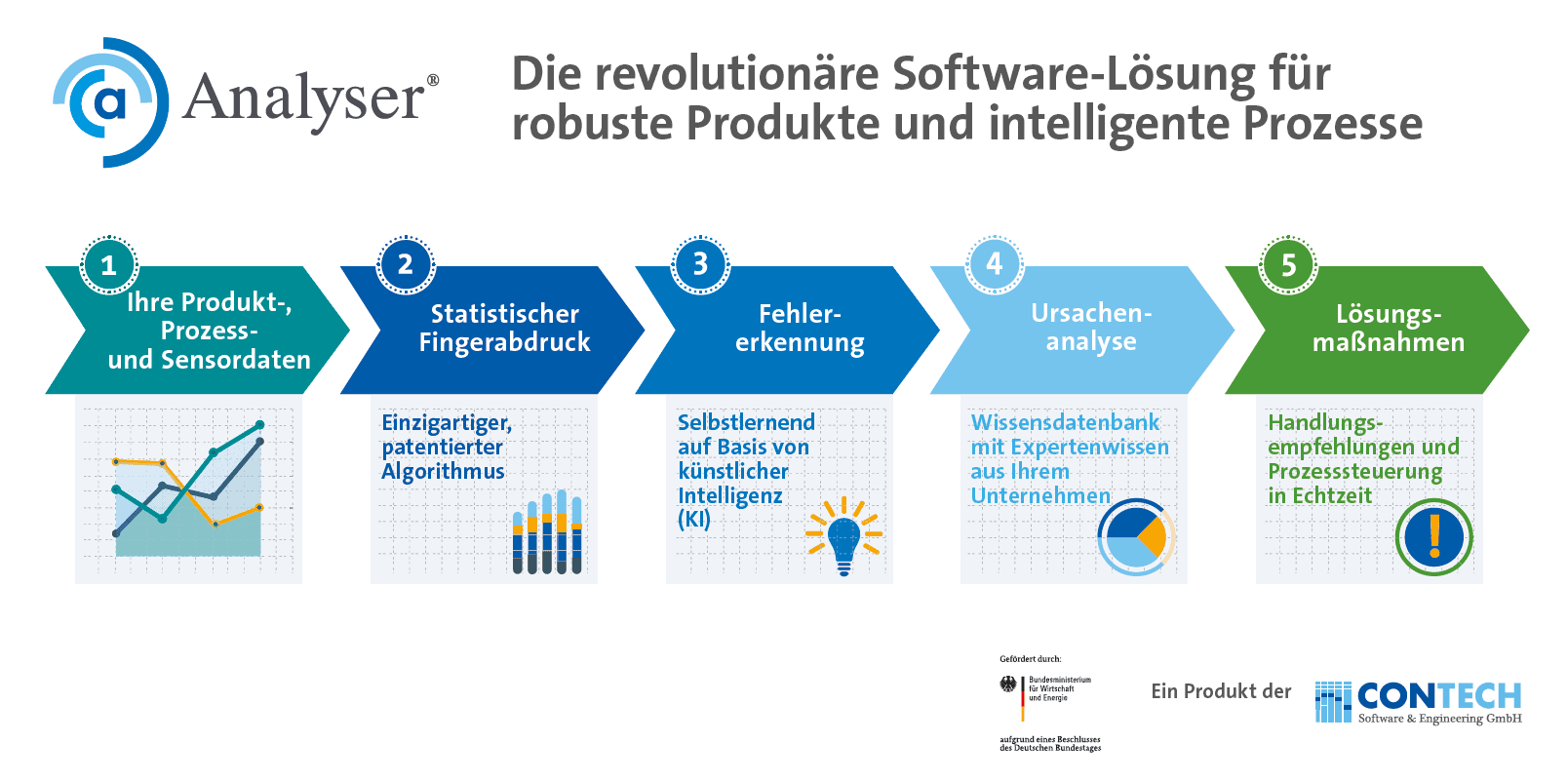
Warum Analyser® ?
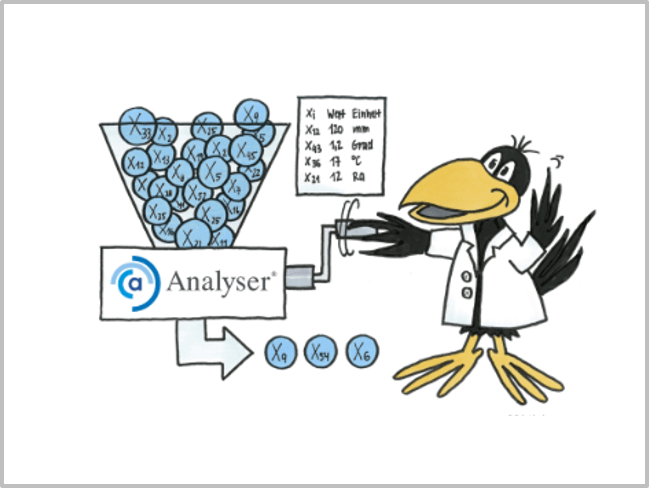
Automatisierte Modellbildung und Stichprobenziehung

Patentierter KI-Algorithmus zur Fehlerbilderkennung
Dank unseres international patentierten Algorithmus werden Fehlerbilder schon mit kleinen Anlernstichproben anhand von Kurvenverläufen in Entwicklung und Produktion präzise erkannt und entsprechende Ursachen und Maßnahmen folgerichtig bestimmt.
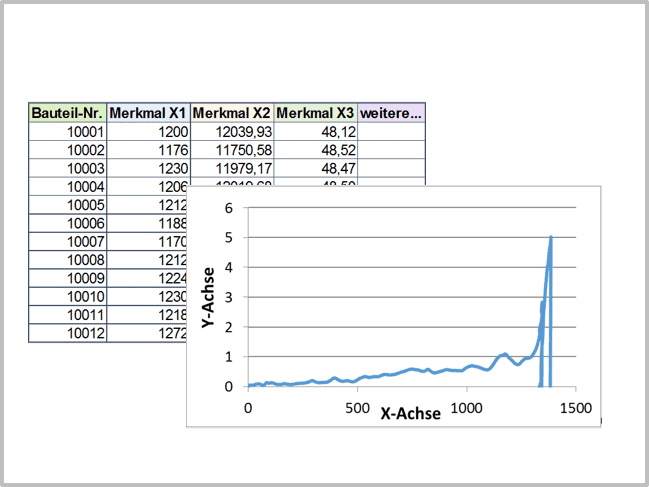
Verarbeitung von Einzelwerten UND Kurvenverläufen für das Vorhersagemodell
Nur mit unserem Verfahren ist es bis dato möglich Kurvenverläufe als Einflussgrößen für die Vorhersagemodelle zu verarbeiten. Erst dadurch können die Einflussgrößen auf den Prozess oder das Produkt exakt bestimmt werden, denn der Root Cause steckt oft in der Verlaufskurve selbst und wird mit einem Einzelwert ungenügend erklärt.
FAQ - Analyser®
- Welcher Algorithmus steckt hinter dem Analyser®?
Das Verfahren basiert auf einer speziellen Kombination von statistischen Methoden, (Parameter-) Modellen und dem einzigartigen, patentierten Algorithmus.
Damit können bestehende Produktvalidierungs- und Prozesskurven und Einzelwerte für robuste Produkte und stabile Prozesse analysiert werden. Ohne dieses patentierte Verfahren ist es bis dato nicht möglich, Kurvenverläufe vollautomatisch zu analysieren, um Fehlerbilder verlässlich zu erkennen. Dazu werden auch Kurvenverläufe als Einflussgrößen für die Vorhersagemodelle (für Predictive Analytics/ Predictive Maintenance) verarbeitet. Erst dadurch können die Einflussgrößen auf den Prozess oder das Produkt exakt bestimmt werden, denn der Root Cause steckt oft in der Verlaufskurve selbst und wird mit einem Einzelwert ungenügend erklärt.
- Wird mit Big-Data-Analysen gearbeitet?
Nein, wir arbeiten mit Stichproben aus einer großen Datenmenge. Die Ziehung der Stichprobe erfolgt sozusagen aus Big Data. Wie die Ziehung der Stichprobe erfolgt, ist Teil unserer Methode aus 14 Jahren Engineering und Six Sigma Erfahrung in über 1000 Projekten.
- Wie erfolgt die Implementierung des Analyser®?
Alle Implementierungsschritte zum Produktionsassistenten und Transferfunktionsmodul finden Sie hier.
- Wie sieht das Netzschema für eine Implementierung aus?
Der Analyser® benötigt zwei virtuelle Maschinen:
- Der Analyser® Server mit einer SQL Datenbank auf Windows 10
- Wenn kein MES- oder Prozessdatenmanagementsystem vorhanden ist: Der IPM 6.0-Server und XLM-Schnittstellenserver mit einer Oracle Datenbank auf Linux (IPM ist ein Prozessdatenmanagementsystem unseres Partners CSP. Mehr Informationen zu unserem Partner finden Sie unter Kooperation)
- In welcher Form müssen meine Daten vorliegen?
- Sensordaten
- Die Daten müssen für eine erfolgreiche Auswertung gelabelt sein
Wir helfen Ihnen dabei die relevanten Einflussgrößen zu bestimmen und messbar zu machen. Außerdem unterstützen wir Sie bei den notwendigen Messsystemanalysen für die weitere Digitalisierung.
- Wo liegt die Künstliche Intelligenz des Analyser®?
Nach einer Teach-In-Phase ist der Analyser® eigenständig dazu fähig, Fehler und entsprechende Fehlerbilder zu erkennen. Zusätzlich enthält das KI-System auch ein Selbstlernmodul bei dem erfolgreiche Maßnahmen rückgemeldet werden. Diese Rückmeldungen werden dann für weitere Analysen berücksichtigt. Somit wird die Analysefähigkeit des Analyser® mit Hilfe der Mitarbeiter und Experten ständig weiterentwickelt und verbessert.
Unser Infomaterial zum Analyser®
- Kurzbeschreibung Analyser® Deutsch: Analyser Kurzbeschreibung
- Kurzbeschreibung Analyser® Englisch: Analyser Short Description
- Leistungsbeschreibung Analyser® Deutsch: Analyser Leistungsbeschreibung
- Leistungsbeschreibung Analyser® Englisch: Analyser Performance Description
Kooperation
CSP
Softwareentwickler sowie Softwareberater für hochwertige und individuelle Lösungen zur Qualitätssicherung in der fertigenden Industrie und zur Datenbankarchivierung.
Die Kooperation mit unserem Partner CSP erfolgt dabei auf Basis von IPM® – ein Integriertes Prozessdatenmanagementsystem, welches herstellerunabhängig alle Mess- und Prozessdaten erfasst und zusammen mit unserem Analyser® frühzeitig Fehler im Produktionsprozess aufdeckt und damit hohe Qualitätsanforderungen sichert.
Bei Unstimmigkeiten alarmiert Sie das System in Echtzeit. So können Sie sofort eingreifen, die Qualität Ihrer Produkte nachhaltig verbessern und sich zuverlässig vor Produktrückrufen oder Imageschäden schützen. IPM sammelt sämtliche Prozessdaten, wie etwa Drehmoment- oder Einpresswerte in einer Lebenslaufakte und gewährleistet selbst nach Jahren den Zugriff, falls Sie diese Informationen für Gesetzgeber oder unternehmensinterne Richtlinien benötigen. www.csp-sw.de
Visual-XSel
Das komplette Tool für Datenanalysen und Methoden nach Six Sigma. Kein anderes Programm vereint derart Statistik mit allen wichtigen Methoden wie Systemanalyse, Fehlerbaumanalyse, DoE, Weibull, Shainin und Six Sigma unter einem Dach.
Visual-XSel ist an den Analyser® angebunden und damit Teil des Analyser®-Prozessdatenmanagement-Paketes. Dabei wird Visual-XSel für die Modellbildung verwendet: So werden für die gesuchten Wirkzusammenhänge die relevanten Einflussfaktoren mit und ohne Wechselwirkung automatisiert ermittelt, die die Produktfunktionalitäten und Prozesse bestmöglich abbilden. www.crgraph.de
Kundenstimmen zu Projekten mit dem Analyser®
Sprechen Sie uns gerne an
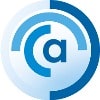
Weitere Informationen
Sie würden gerne mehr über den Analyser® erfahren und ihn live in Aktion sehen? Melden Sie sich einfach zu einem unserer kostenfreien Webinare an. Hier geht’s zur Webinar-Anmeldung
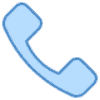
Sie haben noch Fragen?
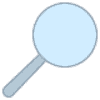
Wir decken Ihre Wirkzusammenhänge auf
Wir bieten Ihnen kostenfrei die Möglichkeit unbekannte Wirkmechanismen und die relevanten Einflussgrößen für Ihre Produkte und Prozesse zu ermitteln. Füllen Sie einfach unser Kontaktformular aus und fordern Sie einen Probedurchlauf an.
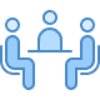
Unser Workshoptag
Wir unterstützen Sie bei Ihrem Digitalisierungsvorhaben: Im Workshop ermitteln wir erste multiple Vorhersagemodelle, damit Sie Ihre Einflussgrößen für nachhaltige Qualität und Kostensenkung aktiv steuern können.